China’s Demographic Shift: Will Cheap Production Move Abroad or Be Replaced by Robots? (27.01.205)
One supplier had a robot that brought the material from the warehouse to production. When speaking to the company’s works council about it, he said that at first he had a negative attitude towards the robot because they cut two warehouse employees after implementation, but then they hired two technicians so that someone is always there around the clock in case there is a malfunction. That put it into perspective a bit, he said. China’s demographic challenges, characterized by a shrinking workforce and a rapidly aging population, present a complex situation that could have profound economic and social impacts. Let’s explore whether cheap production is more likely to shift to other countries or if China will compensate for its demographic decline with robots.
✨Get a Dissertation Research Proposal on this Topic
Fill in the form and we will shortly create and send you the research proposal on "China’s Demographic Shift: Will Cheap Production Move Abroad or Be Replaced by Robots? " for free.
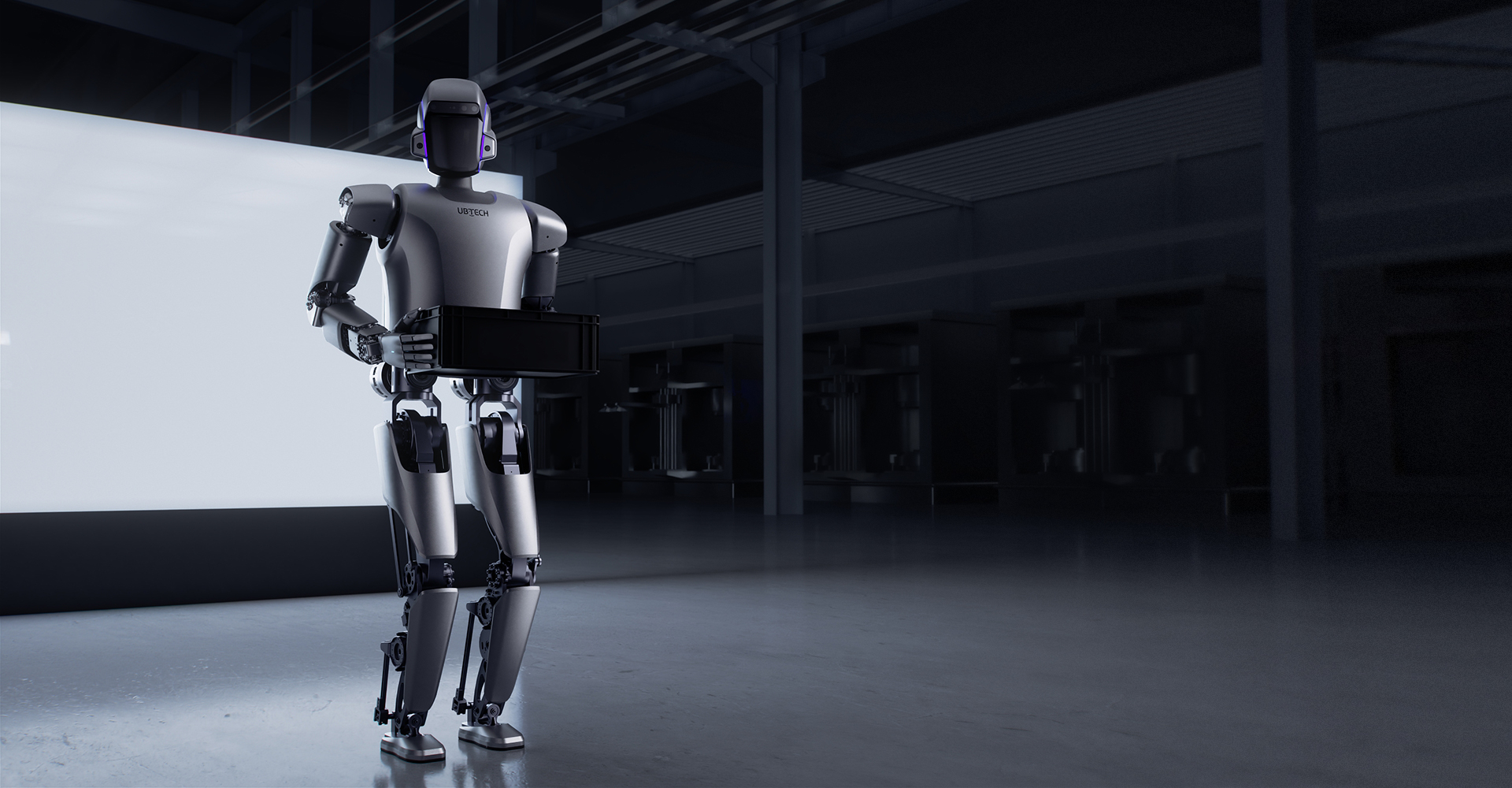
Relocation of Cheap Production to Other Countries
As labor becomes scarcer and wages rise in China, many companies may consider relocating their production facilities to other countries. For example, Southeast Asian nations like Vietnam, Indonesia, and Cambodia are emerging as popular alternatives. These countries have younger populations, lower labor costs, and geographic proximity to existing supply chains in Asia, making them attractive manufacturing hubs.
In addition to Southeast Asia, countries in South Asia, such as India and Bangladesh, and some African nations, such as Ethiopia and Kenya, are becoming increasingly appealing. These regions have large, young workforces and governments eager to attract foreign investments in manufacturing. For Western markets, nearshoring might also become a viable solution, with production moving closer to consumer bases. For instance, Mexico has become a significant option for U.S.-based companies looking to shorten supply chains.
However, relocating production has challenges. Many alternative countries lack the infrastructure, skilled labor, and efficiency that have made China the global leader in manufacturing. While these nations may take on labor-intensive industries like textiles, advanced manufacturing may remain within China’s borders due to its expertise and infrastructure.
Compensation with Robots and Automation
China is already making significant investments in automation and robotics, and this trend is likely to accelerate. As wages increase and the workforce shrinks, companies are turning to advanced robotics to maintain productivity. For instance, China is one of the world’s largest markets for industrial robots, and many companies are automating tasks traditionally done by humans. Industries such as electronics manufacturing (e.g., companies like Foxconn) and automobile production are at the forefront of this shift.
Beyond industrial robots, the Chinese government is investing heavily in artificial intelligence (AI). AI-powered systems are improving efficiency across various industries, including manufacturing, logistics, and healthcare. In addition to factory automation, robots are playing an increasing role in eldercare as China’s population ages. Service robots are being deployed to assist with tasks like health monitoring, companionship, and mobility support.
Automation offers China a strategic advantage because it allows the country to retain control over its supply chain and remain competitive in global markets. However, there are challenges to widespread automation, such as the high initial costs for small and medium-sized enterprises (SMEs), as well as limited adaptability in industries requiring human dexterity or creativity. Additionally, rapid automation could have social consequences, particularly for workers displaced from low-skilled jobs.
Which Is More Likely?
In reality, both scenarios are likely to happen simultaneously. Labor-intensive industries that rely on low wages will gradually move out of China to countries where labor is cheaper. At the same time, China will focus on automating higher-value production processes, enabling it to maintain its status as a global manufacturing leader.
Furthermore, the Chinese government is expected to pursue a dual strategy. On one hand, it will continue incentivizing automation and technological innovation. On the other hand, it will introduce policies to mitigate the impact of population decline, such as improving healthcare for the elderly, encouraging higher birth rates, and increasing retirement ages to keep older workers in the labor force.
Conclusion
While labor-intensive industries are likely to relocate to other countries, particularly in Southeast Asia, South Asia, and parts of Africa, China’s significant investment in robotics and automation will allow it to adapt to its demographic challenges. By automating high-value manufacturing and leveraging advanced technologies, China can sustain its economic growth while addressing its shrinking workforce and aging population. Ultimately, this combination of relocation and automation will shape the future of global production.
PS: From Job Loss to Opportunity: How Automation Reshaped Roles in a Manufacturing Plant
The implementation of robotics in manufacturing and logistics often evokes a range of reactions, particularly from employees and works councils concerned about job security. One notable example comes from a supplier that introduced a robot specifically designed to transport materials from the warehouse to the production floor. At first glance, the robot seemed like a clear case of automation replacing human workers, as the company decided to cut two warehouse jobs shortly after the robot’s implementation.
When discussing this change with the company’s works council, a representative admitted that the initial reaction to the robot was negative. Employees and the council viewed it as a direct threat to job security, which fueled skepticism and resistance toward further automation. However, the situation evolved over time, and the council’s perspective shifted.
Although the robot streamlined material handling and eliminated two roles, the company soon realized that maintaining and operating the robotic system required additional technical expertise. To address this, the company hired two technicians to ensure that someone was always available around the clock to handle potential malfunctions, perform preventive maintenance, and troubleshoot issues with the robot.
This shift highlighted a significant nuance in the automation debate: while robots can displace certain roles, they often create new opportunities for skilled jobs in areas like robotics maintenance, programming, and system monitoring. The representative from the works council admitted that this reframed their view of the situation. While the two warehouse jobs were indeed lost, the addition of two technical roles provided new opportunities for workers, albeit requiring different skill sets.
This example underscores the complexity of automation’s impact on the workforce. It is not a simple matter of machines replacing humans but rather a reconfiguration of roles. Workers whose jobs are displaced by automation may face challenges if they lack the technical skills needed for new roles, making training and reskilling critical components of a smooth transition. The company’s proactive approach to hiring technicians demonstrated an effort to balance efficiency with workforce sustainability.
Ultimately, this story illustrates that while automation can introduce disruptions, it can also drive opportunities for new types of employment. The key lies in how companies and employees adapt to these changes, with an emphasis on training, collaboration, and communication to mitigate fears and foster a constructive outlook on the integration of technology.
About ECEBiS
At ECEBiS you are going to understand what will change the trajectory of the financial industry. You will develop a transversal view on the forces that are shaping the future financial industry.
From payments and lending to investment and money management, tech providers are actively shaping the future of the financial landscape - even pushing the boundaries of currency itself. You might evaluate the impact of robo-advising on health management and examine portfolio recommendations from a diversified set of RAs and attempt to identify the factors behind proposed splits between asset classes.
ECEBiS is a platform in academic research on new business models and innovative products. We investigate in fast moving sectors that are reshaping the financial world of tomorrow and pioneering new ways of doing business. We want to attract outstanding ECEBiS students in finance with experiences and exposures, who intend to
Doctorate of Business Administration (DBA) in Finance (online, 3 years part-time)
develop knowledge on challenges that shape the future of financial industry
engage with a program that offers the convenience of online learning with the benefits of accreditation and global reach.
raise awareness on the importance of fintech and sustainability in finance
identify the best practices in the financial industry to spread positive changes
Go beyond the virtual classroom and network with other ambitious executives and entrepreneurs as you expand your credibility and expertise in the world’s most transformative fields.